Part one of the two-part ‘Lean Validation’ series, “Achieving Lean Validation in GxP Organizations” explores Lean, it’s origins and how to eliminate waste through paperless validation software.
Read | Part Two – Managing value through lean validation
Origins of the lean method
The term ‘Lean’, describes a methodology for streamlining processes, with the aim of increasing revenue, reducing cost and eliminating waste, while enhancing customer satisfaction. The application of ‘Lean Methods’ ultimately results in a process that is more efficient, economical and faster whilst continuing to deliver a product of satisfactory quality.
The concept of Lean was first established by the Toyota Corporation in the early 1950’s, who while researching to develop a new system of production, began studying supermarkets’ product stocking behaviors. Toyota observed supermarkets replenishing stock, ‘just enough’ ‘just in time’ before demand was required. Applying this technique to the factory floor, Toyota produced just enough parts in the first phase of manufacturing to replace what was used in the second phase of manufacturing, enabling Toyota to eliminate waste and allowing the company to operate on a tighter budget.
Becoming known as the ‘Toyota Production System, this ‘Just in Time’ approach to inventory management provided inventory per production demand using the ‘Kanban’ demand scheduling method.
Studying other companies’ manufacturing processes, Toyota also observed production often continued undisrupted, despite defects occurring, with these defects resolved only after a product rolled off a line.
Seeing opportunity to address this issue, Toyota introduced a cord above every station, when a defect was identified the line was stopped and a team worked on the defect. Toyota correctly believed this encouraged workers and machines to identify defects on a more frequent basis, it also led to a dramatic reduction in defects. With these continuous improvements in place, Toyota quickly gained recognition for being a producer of reliable and affordable cars, enhancing its overall position in the market.
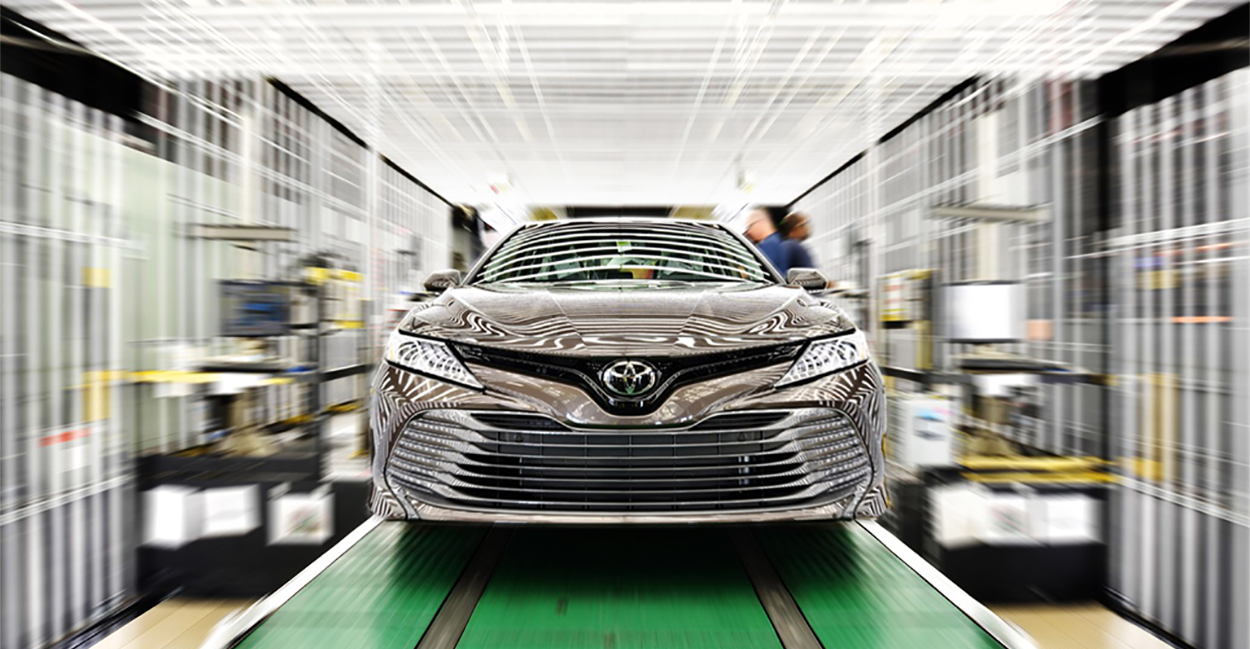
Toyota’s lean mantra: ‘Muda, Mura, Muri
Like Toyota, many organizations are affected by inefficiencies, most often in the forms of either waste, variation or overburden – what Toyota labelled, ‘Muda’, ‘Mura’ and ‘Muri.’
Muda: Waste
Meaning ‘wastefulness’, under which there are eight categories of waste. These types of waste can be most easily identified using the abbreviation TIMWOODS representing:
- 1 | Transport
- 2 | Inventory
- 3 | Motion
- 4 | Waiting
- 5 | Overproduction
- 6 | Over processing
- 7 | Defects
- 8 | Skills Under-use
Mura: Variation
Meaning inconsistent outcomes or expectations, Mura can be avoided and ultimately eliminated, through the ‘Just in Time’ Kanban concept.
Muri: Overburden
Meaning unnecessary or unreasonable overloading of people, equipment, and systems. In some cases, this can be caused by the excessive removal of Muda (waste) from a process.
Eliminating ‘TIMWOODS’ through paperless validation
Paperless validation software delivers significant reductions to, if not complete removal of waste from each of the eight categories of waste:
Transport
Transport is described as the movement of people, products, and information from one location to another that does not add value. During a paper- based validation a protocol can potentially be transported between multiple departments in multiple different buildings for final approval. By using KneatGx an organization can eliminate this waste at a click of a button. As witnessed during the COVID19 pandemic, organizations that utilize KneatGx were less impacted working from home compared to others. Through KneatGx approvers could still review/approve qualifications from home ensuring manufacturing could continue.
Inventory
Inventory is described as excess products and materials not being processed, for example, building up unnecessary stocks. Completing validation activities through a paper-based process leads to countless approved protocols needing secure storage while ensuring they can be found when required. KneatGx eliminates this build-up of approved protocols. All validation protocols can be developed, executed, maintained, stored, and retrieved at a click of a button within KneatGx.
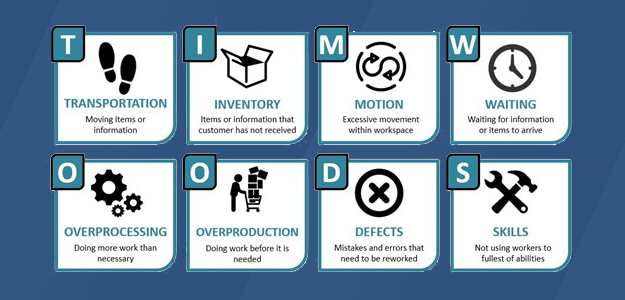
Motion
Motion is the unnecessary movements taken by people walking to retrieve equipment, protocols or reports that should be located closer to the point-of-use. KneatGx enables qualifications to be executed using a tablet computer on the manufacturing floor in real time. This feature of KneatGx eliminates the countless hours wasted by engineers during a qualification walking from equipment to desk and back to equipment with pages of the protocol for execution. Again, this eliminates waste and enhances the organizations validation process.
Waiting
Waiting within an organization can be described as waiting for information, items, approval or other processes or people. Qualification activities cannot be executed until the protocol is approved and present on the manufacturing line/floor. KneatGx reduces this waiting time by allowing for approval to take place through the application, once the protocol is approved it can be executed immediately. There is no waiting for the protocol to be transported from the office to the area where the qualification is taking place.
Over production
Over-production is the development of outputs that were not requested and is often described as one of the worst of the seven wastes of lean manufacturing. A cost associated with over- production is in relation to the storage and movement of the inventory that was created. As discussed above approved paper qualification protocols require a secure storage space. By using Kneat Gx, countless protocols can be developed when required and stored securely within the application.
KneatGx eliminates this build-up of approved protocols. All validation protocols can be developed, executed, maintained, stored, and retrieved at a click of a button within KneatGx.
Over processing
Over processing is described as completing more work than is required. Over processing within a paper-based validation process can be described as the over processing of paperwork. Multiple approval levels of a validation protocol can lead to over processing of paperwork, KneatGx enables the approval process to happen at the one level. The functionality of KneatGx also allows for protocols to be issued for electronic review to all key stakeholders at once, comments from all reviewer and the protocol can be issued for review to all approvers once the comments are addressed. This eliminates the back and forth between departments, hence, eliminating over processing paperwork.
Defects
Defects within an organization is defined as failing to produce quality outputs the first- time round. By using KneatGx for execution of validation protocols incorrect data entries can be dramatically reduced. KneatGx offers functionality where drop-down menus can be utilized during qualification activities, enabling a reduction in the number of incorrect data entries. This reduction also leads to less re-work in the approval cycle, saving organizations valuable man hours.
Skills (under-utilization of)
This waste is depicted as the failure to use the skills and capabilities of staff. KneatGx allows for multiple review cycles to take place prior to template or protocol approval, incorporating the reviews from all relevant subject matter experts from various departments. The functionality within KneatGx allows for comments to be added and addressed in a timely fashion ensuring the needs of all departments are met, this is often lost in an overburden paper-based process.
‘Muda, Mura, and Muri’ consume GxP organizations ‘precious resources every day. By applying lean methodologies across the lifecycle of any process, your organization can find and deliver reductions in cost and shorten its time to market. Kneat eliminates ‘Muda, Mura, and Muri’ through the life cycle of any validation process, by reducing organizations waste.