As the Pharmaceutical industry adopts Industry 4.0 as its own Pharma 4.0 , automation becomes essential driver for digital transformation. Being a regulated industry, the validation of automated systems is mandatory to ensure regulatory compliance, operational efficiency, and product quality.
In the article below we take a comprehensive look at the general principles of validating automated systems and some of the unique challenges pertaining to Delta V.
Key objectives of validation in automated systems
Like any other system, the objective of validation in automated systems is to ensure that the system operates as intended, complies with regulatory standards, and delivers reliable performance. The list of the deliverables does not change, nor do the objectives. The key objectives of validation in automated systems include:
- Ensuring product quality and safety
- Maintaining regulatory compliance
- Minimizing operational risks
- Enhancing process efficiency and productivity
- Facilitating effective change management
Overview of Delta V systems
Delta V, engineered by Emerson Process Management, stands out as a premier distributed control system (DCS) in the automation and process control industry. It’s recognized for its broad applications across numerous sectors. Delta V Systems are highly regarded for their robust capabilities, securing a significant position in the automation market. They are essential for seamless process automation, providing flexible and scalable solutions that ensure continuous operations and remote system access.
In the pharmaceutical manufacturing arena, Delta V is instrumental in producing a wide array of drugs, supporting the advancement of Pharma 4.0 with its superior data management capabilities. Its advanced control systems are not only pivotal for maintaining safety and efficiency in the petrochemical and nuclear fields but are also adept at meeting the demands of today’s industrial challenges. With its solid construction and enhanced cybersecurity measures, Delta V Systems are vital for maintaining high standards of operational excellence and control in various industries.
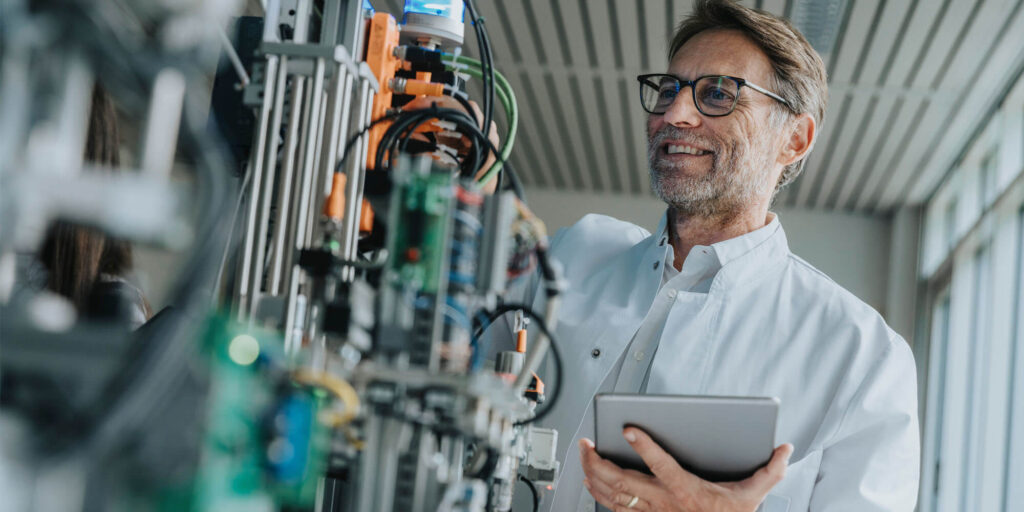
Steps in the validation process
The validation of any system will follow a standard validation process, and assuming that you are aware of this, let’s look at how validation of an automation system differs from a standard computerized system.
The key differences in validating automated systems versus standard applications lie in the increased complexity, risk, and regulatory requirements associated with automated systems. Automated systems require more rigorous validation approaches, intelligent techniques, and extensive documentation compared to standard applications.
In the table below, we also look at all deliverables which are typically required.
Table 1 Automated System Validation Vs Standard Application Validation
Step | Automated System Validation | Standard Application Validation |
---|---|---|
User Requirements Specification (URS) | Detailed URS capturing specific user requirements for both hardware and software components, often involving complex interactions and integrations. | URS typically focuses on software requirements, with less emphasis on hardware interactions. |
Functional Design Specification (FDS) | Elaborates on URS by detailing security groups, control strategies, and custom configurations required for automated systems. | FDS focuses on software functionalities and user interactions, with simpler security and configuration requirements. |
Hardware Design Specification (HDS) | Captures detailed specifications of all hardware components, including part numbers and configurations. | Generally, not required unless the application involves specific hardware dependencies. |
Software Design Specification (SDS) | Includes detailed configuration settings for software components to meet the requirements specified in the FDS. | Focuses on software architecture and design, with less emphasis on configuration settings. |
Risk Assessment | Comprehensive risk assessment due to the complexity and potential impact on processes, product quality, and safety. | Risk assessment is simpler, focusing on software-related risks and user scenarios. |
Configuration Management | Rigorous configuration management to control and document changes to both hardware and software components. | Configuration management is typically less complex, focusing on software changes. |
Testing and Verification | Extensive testing, including interface testing, data mapping, error handling, and verification of custom configurations and control strategies. | Testing focuses on functional requirements, user scenarios, and regression testing. |
Validation Techniques | Utilizes intelligent validation techniques such as simulation, AI-based testing, and scenario-based testing to handle complexity and non-deterministic behavior. | Traditional validation techniques like functional testing and regression testing are sufficient. |
Installation Qualification (IQ) | Verifies that the system is installed and configured according to design documentation, including hardware and software components. | Ensures that the application is installed and running on the intended hardware/software environment. Normally a lean document. |
Operational Qualification (OQ) | Tests the system to ensure it operates as intended under specified conditions, including hardware-software interactions. | Focuses on verifying that the software operates as intended under specified conditions. |
Performance Qualification (PQ) | Confirms that the system performs consistently and reliably in a production environment, considering both hardware and software performance. | Ensures that the software performs consistently and reliably in a production environment. |
Regulatory Compliance | Must comply with specific regulations and standards such as FDA, ISO, and GAMP, requiring extensive documentation and traceability. | Same or as applicable however, ISO requirements are not so often referred. |
Documentation and Reporting | Comprehensive documentation and reporting are crucial for traceability, auditing, and demonstrating compliance with regulations and industry standards. | Documentation and reporting requirements are less extensive, focusing on software development and testing processes. |
Challenges in validating Delta V systems
Delta V is a highly advanced Distributed Control System (DCS) designed to enhance plant operations through predictive technologies and intuitive interfaces. It stands out in the automation landscape due to several unique features and capabilities, but these also introduce specific challenges that need to be addressed during validation and implementation.
Table 2 Challenges and Strategies in Delta V Validation
Challenge | Technical Details | Strategies to Handle |
---|---|---|
System Complexity | Delta V systems involve intricate hardware and software configurations, including controllers, I/O modules, and communication interfaces such as HART, FOUNDATION fieldbus, and Profibus DP. | Implement modular validation approaches, focusing on individual components and their interactions. Use simulation tools to test complex configurations before deployment. |
Integration with Third-Party Systems | Delta V systems often integrate with MES, ERP, and other third-party systems using interfaces like OPC, Modbus, and Ethernet/IP. | Conduct thorough interface testing and validation. Use standardized communication protocols, ensure robust data mapping, and error handling mechanisms. |
Customization and Configuration | Delta V systems are highly configurable, allowing for custom control strategies, batch processing, and safety instrumented functions. | Develop detailed configuration management plans. Use version control systems to track changes and ensure that custom configurations are thoroughly tested and documented. |
Change Management | Ensuring that changes to the Delta V system, including software updates, hardware modifications, or process changes, are properly validated and documented. | Implement a rigorous change management process. Use automated tools for impact analysis and regression testing to ensure that changes do not adversely affect system performance. |
Regulatory Compliance | Adhering to various regulatory guidelines and industry standards, such as FDA regulations (21 CFR Part 11, cGMP) and ISA standards. | Maintain comprehensive documentation and traceability. Conduct regular audits and reviews to ensure ongoing compliance. Use validation templates and checklists to streamline the process. |
Regulatory considerations
Validating Delta V systems often involves compliance with various regulatory bodies and industry standards, depending on the specific business use and application. Some of the key regulatory considerations include:
- FDA Regulations (21 CFR Part 11, cGMP): For pharmaceutical and biotechnology industries, Delta V systems must comply with FDA regulations for electronic records and electronic signatures, as well as current Good Manufacturing Practices (cGMP).
- ISO Standards (ISO 9001, ISO 14971): Delta V systems used in regulated industries may need to comply with relevant ISO standards for quality management and risk management.
- Industry-Specific Standards (ISA, GAMP): Certain industries, such as process control and automation, may require adherence to standards set by organizations like the International Society of Automation (ISA) or the International Society for Pharmaceutical Engineering’s (ISPE) Good Automated Manufacturing Practice (GAMP) guidelines.
Best practices for effective validation
- Adopting a Risk-Based Approach: Prioritizing validation efforts based on risk assessments and focusing on critical system components and processes.
- Leveraging Automation Tools: Utilizing automated testing tools and scripts to streamline the validation process and improve efficiency.
- Establishing Clear Roles and Responsibilities: Defining clear roles and responsibilities for all stakeholders involved in the validation process, including system owners, validation teams, and subject matter experts.
- Maintaining Comprehensive Documentation: Documenting all validation activities, test results, deviations, and change controls to ensure traceability and compliance.
- Fostering Collaboration and Communication: Encouraging open communication and collaboration among cross-functional teams, including process engineers, automation experts, and validation specialists.
- Continuous Improvement: Regularly reviewing and updating validation processes, incorporating lessons learned and industry best practices.
Conclusion
Validating Delta V systems is a critical endeavor that requires a comprehensive understanding of the validation process, regulatory requirements, and best practices. By following a structured approach, addressing unique challenges, and adhering to regulatory guidelines, organizations can ensure the integrity, reliability, and compliance of their Delta V systems. Effective validation not only minimizes operational risks but also enhances process efficiency, product quality, and overall operational excellence.
Suggested Reading and References
- “Validation of Automated Systems in the Pharmaceutical Industry” by the International Society for Pharmaceutical Engineering (ISPE)
- “Good Automated Manufacturing Practice (GAMP) Guide” by the International Society for Pharmaceutical Engineering (ISPE)
- “21 CFR Part 11: Electronic Records; Electronic Signatures” by the U.S. Food and Drug Administration (FDA)
- “ISA-TR88.00.02: Machine and Unit Control Systems Integration” by the International Society of Automation (ISA)
- “ISO 9001: Quality Management Systems – Requirements” by the International Organization for Standardization (ISO)
- “ISO 14971: Medical Devices – Application of Risk Management to Medical Devices” by the International Organization for Standardization (ISO)
- “Delta V Validation Resources” by Emerson Process Management