Commissioning and qualification, C&Q, CQV…no matter how you spell it, this function is crucial to establishing capital expenditure (CAPEX) projects and day-to-day operations of highly regulated manufacturing. Without commissioning and qualification, quite simply, you can’t produce.
In this blog, we explore exactly what is commissioning and qualification (C&Q), often referred to as CQV (commissioning, qualification, and validation). These two key processes are critical to ensuring systems and equipment function correctly and consistently. They provide assurance for not only product safety but are also required for regulatory compliance. This makes them an integral part of the success of any manufacturer.
Understanding CQV
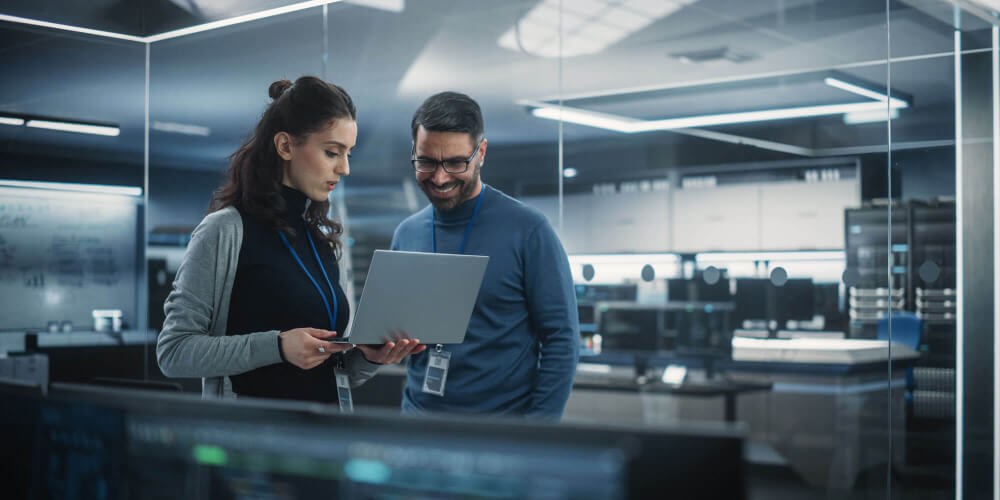
We’ll start with a quick overview of CQV:
Commissioning: A well-planned, documented approach to the start-up and turnover of facilities, systems, and equipment to the end user.
Qualification: The documented verification that all aspects of a facility, utility, or equipment that can affect product quality adhere to approved specifications.
Validation: Establishing documented evidence which provides a high degree of assurance that a specific process will consistently produce a product meeting its pre-determined specifications and quality attributes.
Commissioning is the systematic process of verifying and documenting that facilities, systems, and equipment are designed, installed, tested, and capable of being operated and maintained according to the operational requirements of the owner. It covers a broad spectrum, including design reviews, installation checks, and performance testing.
Qualification, on the other hand, is a subset of commissioning focused specifically on validating that equipment and systems are fit for their intended purpose. Qualification is often broken down into several stages:
- Design qualification (DQ): Verifies that the design meets all regulatory, client, and company requirements.
- Installation qualification (IQ): Ensures that systems and equipment are installed according to the design specifications and manufacturer’s recommendations.
- Operational qualification (OQ): Confirms that the equipment operates within defined parameters and performs as expected under normal operating conditions.
- Performance qualification (PQ): Validates that the system performs effectively and reproducibly under real-world conditions.
Importantly, commissioning is primarily concerned with the facilities, equipment, and instruments used in manufacturing, whereas validation and qualification are concerned with product quality. This brings qualification and validation under the specter of regulatory bodies, whereas commissioning is not.
While every company will have slightly different ways of executing CQV, the typical process sees commissioning activities occur, then qualification as part of ongoing validation.
The importance of CQV
- Regulatory Compliance: Regulatory bodies like the FDA (Food and Drug Administration) and EMA (European Medicines Agency) require strict adherence to guidelines to ensure product safety and efficacy. CQV processes provide documented evidence that systems meet these regulatory standards.
- Risk Mitigation: Thorough commissioning and qualification help identify and rectify potential issues early in the lifecycle of a system or piece of equipment. This reduces the risk of failures that could lead to costly recalls, downtime, or safety incidents.
- Quality Assurance: CQV ensures all systems and processes are capable of consistently producing products that meet predefined quality criteria, thus maintaining the integrity of the product and the trust of consumers.
- Operational Efficiency: By validating that systems operate as intended, companies can optimize performance, reduce waste, and enhance overall operational efficiency.
How to implement CQV
The implementation of commissioning and qualification processes typically follows a structured approach:
- Planning: Develop a comprehensive CQV plan that outlines the scope, objectives, responsibilities, and timelines. This plan should align with regulatory requirements and industry best practices.
- Design Review: Conduct design reviews to ensure that the system or equipment design meets all necessary requirements. This includes reviewing design documents, specifications, and vendor information.
- Installation Verification: During IQ, inspect the installation to ensure it conforms to the design specifications. Document all findings and ensure that any deviations are addressed.
- Operational Testing: Perform OQ by running tests to verify that the system operates as expected under normal conditions. This involves checking controls, alarms, interlocks, and other operational parameters.
- Performance Validation: Conduct PQ by testing the system under actual operating conditions to ensure it performs consistently and reliably. This stage often includes running production batches or performing process simulations.
- Documentation: Maintain thorough documentation throughout the CQV process. This includes test protocols, reports, deviation logs, and any corrective actions taken. Proper documentation is crucial for regulatory audits and inspections.
- Review and Approval: Have all CQV documentation reviewed and approved by qualified personnel. This typically involves quality assurance (QA) teams and regulatory affairs specialists to ensure compliance with all relevant standards.
CQV challenges and how to overcome them
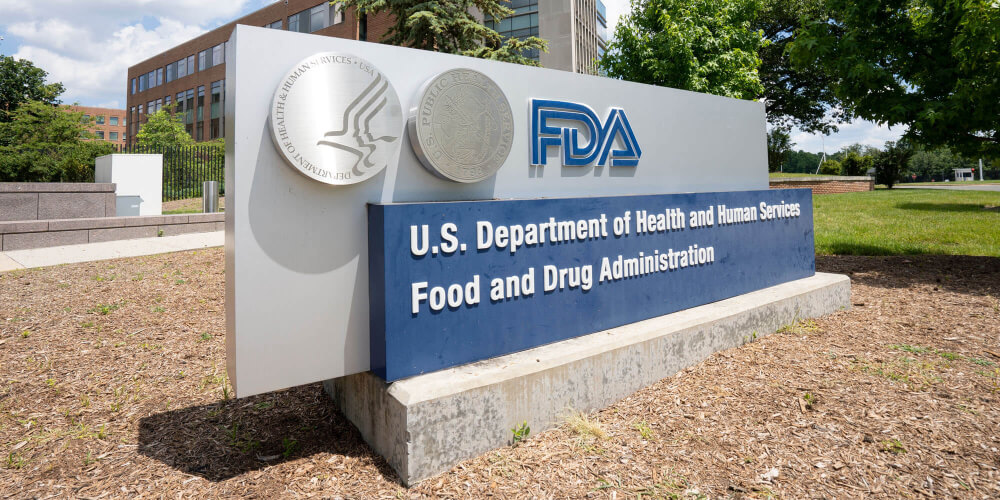
Document volume
The significant volume of documents generated during CQV takes time and energy, demands a storage or management solution , and increases the risk of human error in all stages. There’s no way around the need for extensive documentation, however some steps may be removed or streamlined through well-reasoned planning and process mapping.
Leveraging commissioning test results and standardizing processes where possible will help to decrease the volume of documentation required for effective CQV.
Thorough planning and compliant documentation are a moot point if you can’t find the very documents you worked so hard to build. Paper-based processes are particularly vulnerable to accessibility issues, as it takes time to retrieve documents from storage, assuming they aren’t lost outright. Commissioning documents are particularly vulnerable to ineffective management because they don’t have the same regulatory requirements associated with them.
Regulatory and operational differences
As commissioning focuses on sites and equipment rather than product quality and patient health, the typical regulatory bodies for life sciences — the U.S. Food and Drug Administration (FDA) and European Medicines Agency (EMA) in Europe — don’t get overly involved with this part of manufacturing. Many companies choose to align with guidelines recommended by industry groups such as the International Society for Pharmaceutical Engineering (ISPE). Without an overarching set of criteria, companies have disparate approaches, often varying from site to site or even team to team.
This results in documentation that meets commissioning goals but isn’t fit to provide more detailed information necessary for qualification or validation. It may also lack the data integrity standards required by regulatory bodies for such activities.
Many companies address this by imposing their own standards on commissioning. The ISPE has published guidance regarding CQV , which aims to establish a more integrated approach to commissioning and qualification, resulting in more efficient and less costly programs. This guidance, at a high level, recommends commissioning be fully documented and official, more in line with how qualification or validation teams approach their work. Companies can standardize commissioning from the top down, but this isn’t always possible.
Disconnect between C&Q teams
Not every aspect of CQV is performed by the same team and there can be duplicated work if processes aren’t thought through. For example, testing performed during the initial commissioning phase can provide data that can be used in future qualification, but only if it meets the more intense rigor associated with qualification.
When diligently documented, tests run during commissioning and can be used in later qualification activities to improve right first-time tests, remove redundant steps, and ultimately reduce turnover time. For example, when conducting a commissioning test on a heater, testing for specific temperature ranges, rather than documenting if it simply “gets hot,” this data could then be useful during the qualification process. Some caveats:
- Commissioning documents for direct impact systems never replaces the need for qualification tests.
- To be effective, commissioning documents must meet qualification regulatory standards, including ALCOA+ principles such as wet or protected signatures.
- Processes should be in place to ensure that leveraged documents remain current and accessible.
A well-reasoned commissioning plan is necessary to ensure activities can be leveraged later in the validation process. Detailed Factory Acceptance Testing (FAT) , Site Acceptance Testing (SAT), and User Requirement Specifications (URS) documents should be designed, used, and traced. Detailed documents can provide confidence in equipment, potentially reducing the need for repeat testing.
Using digital validation for CQV
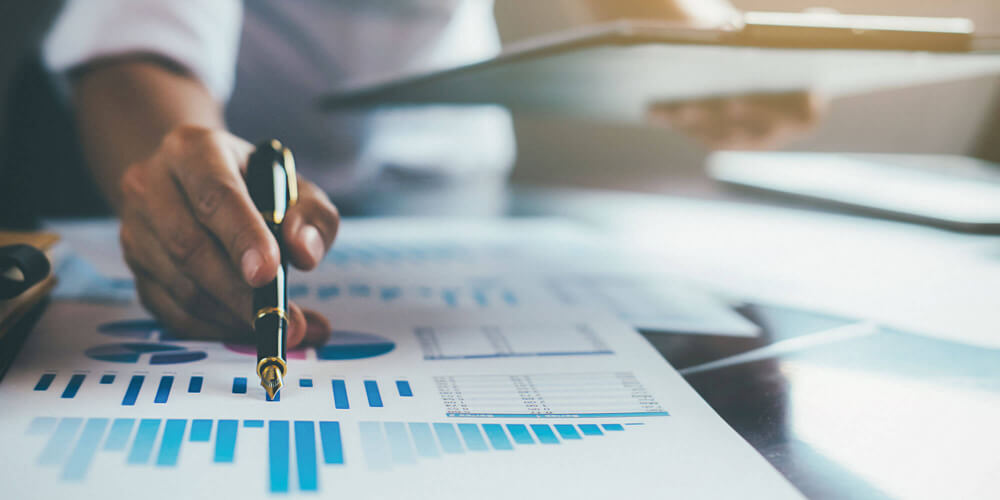
To alleviate the burden of handling massive amounts of documents, sharing complex data, and establishing repeatable best practices, companies should look to digitalize their CQV practices .
A good digital solution can seamlessly scale across an organization, making standardization easier to deploy in global worksites. When sites are in alignment, CQV is more efficient, as sites:
- Execute activities using the same documentation, making oversight easier
- Operate under the same timelines, leading to greater predictability
- Can begin projects with greater certainty in what tests are needed, what documentation is required, and who is responsible for signoffs
You can learn how to transform your CQV processes in The Digital C&Q Guide, available here . If you’re looking for help with your CQV needs or validation in general, Kneat is the leading digital validation solution for eight of the Top 10 life sciences companies.